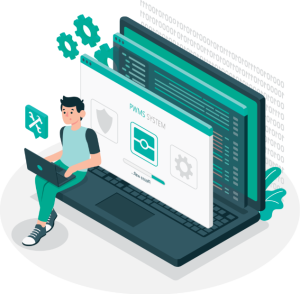
The purchase and procurement phase in a project with an EPC approach, is one of the main phases of the project, which is directly linked to the engineering phase (as a commodity customer) and the construction and execution phases (as a commodity requester).
The PPMS (Procurement Project Management System) software is a comprehensive system for information management and activity control in the procurement phase of large industrial projects, which embraces all purchase and supply processes of a project as follows:
Providing the purchase package
Upon collecting the MTO and MR documents of a commodity or equipment in the engineering unit, the procurement team starts its job. The documents provided by the engineering team, along with other relevant documents such as the maps and technical data, are attached to the purchase request and later sent to the PPMS software via the EDMS software. At this stage, the procurement team examines the documents imported into the PPMS software, creates a purchase package, and uploads all relevant documents in the PPMS software. During the process of purchasing commodities or equipment needed by the employer or the organization, the documents include all the assessment forms of the companies, NDA (non-disclosure agreement) document, tender documents, commodity purchase and supply instructions, standards, inspection instructions, list of the manufacturer and vendor companies, etc.
Identifying the vendor companies
Upon receiving the purchase documents from the engineering team and preparing its own documents, the procurement team begins the phase of identifying the vendor or manufacturer companies of the required product.
In almost all industries, there is a comprehensive list known as the Approved Vendors List or AVL that includes all the companies providing the relevant services in each field. The AVL contains a list of different vendor and manufacturer companies or their representatives, the competency of whom has been previously evaluated and approved by the employer through a specific process. The AVL is indeed a reference for selecting the companies that provided the services intended by the employer. Besides, the companies themselves can, assess, identify and approve the new companies to be included in the AVL list, or select a new list of the manufacturers and vendors for their own organization, and import it into the PPMS software.
Holding tenders and receiving bids (proposals)
Once the manufacturer and vendor companies are identified, it is time to select the intended company through holding a tender. This phase includes a detailed process with different activities, during which registering all the details are of high significance.
The transactions that occur during the process of selecting the manufacturer or supplier of the commodity by the procurement team include: selecting the companies from the AVL list, obtaining the necessary approvals to invite the selected companies to participate in the tender, announcing and distributing the tender documents, obtaining the document classification certificate, sending the technical information and maps to further examine the companies, holding query sessions (question-and-answer sessions) and recording the obtained results, receiving the technical and financial bids (proposals), and examining the bids in all technical, financial, …fields.
In the Technical Clarification phase or final selection of the manufacturer or vendor company, the technical and financial proposals (bids) of the supplier companies are examined. This phase involves the exchange of information between the bidder companies and the employer (buyer) through the project procurement team and with collaboration with the engineering team. The engineering team, as the third dimension of this process, will be present until the technical approval or rejection of the vendor’s proposal.
Selecting the winner
The next step in the Procurement Project Management System is the winner selection phase, in which the procurement team sends the bid report along with a summery on tender’s documents and correspondences, to the organization’s decision-making authority (e.g. the trading commission) in order to select the winner of the tender.
Setting the contract
Selecting the winner is followed by setting the contract in the software. One of the features of this software is its capability to define the details of the contract, including the payment conditions, guarantees, commitments, etc., as well as setting the contract appendices in accordance with the files uploaded during all the previous steps.
Fabrication and inspection phases
Once the contract is signed by the two parties, Kick-off Meeting is held to begin the practical phases of the fabrication or purchase of the commodity. During the commodity fabrication or supply process, activities such as receiving the work progress report from the manufacturer/vendor company, financial payments, etc. are managed by the software.
Furthermore, in the commodity fabrication contracts there is a highly important process named inspection that starts with raw material supply and fabrication process. During all stages of fabrication, in addition to submitting a report, the manufacturer is obliged to provide Inspection Notification for the employer and the project agents inspection. Aside from receiving regular reports, the employer can visit the site and compare the project progress with instructions given and grant final approval.
There are mainly four types of inspection performed by the inspection team in a project:
- Raw material inspection
- Fabrication inspection
- Final acceptance test
- Pre-shipment inspection
In the Engineering Phase, the engineering team announces the ITP (Inspection Test Plan) of each commodity, as one of the technical attachments of the purchase request, to the procurement team and the manufacturer company. At all stages of construction, the employer’s inspectors or the employer’s inspection companies (Third Party) can inspect and test the goods under construction according to the instructions of ITP ,and present the results including the inspection report, NCR and… to the employer.
Before the shipment phase and once the fabrication is complete, the vendor company creates a Packing List of all portable items. Creating the Packing List is highly important for controlling the fabricated or non-fabricated items, informing the warehouse of the items that are ready for shipment and delivery, and most importantly informing the project manager of the proper installation and fabrication program with regard to the warehouse input.
Shipment phase
The shipping process begins as soon as the Packing list is ready. Depending on the volume, weight, financial value, and shipment type (e.g. foreign or domestic shipment, land, marine, or air shipment), this process includes various activities recording of which is very important in the PPMS system. Various documents including the permissions, the customs documents, the loading, shipment, and unloading documents, relevant invoices, and tens of other documents are all created in this phase.
Delivery of items to the site warehouse
Delivery of the items to the site warehouse is the final step of the purchase (Procurement) phase. Once the items are delivered to the project warehouse, the purchase process is finished and the storage process is started. Processes such as OPI, preparation of OSD tables, and eventually registration of MRR or MRS documents will be explained in the warehouse section.
Capabilities of PMS software in various procurement processes
Purchase (procurement) engineering
- Defining the commodity purchase (procurement) and supply as a project
- Recognizing the purchase (procurement) documents in the engineering module under the MR, MTO, TBE, and TBA categories
- Defining the items related to the MR and their number (BOM)
- Organizing the technical attachments of the purchase request including Datasheets, Computations, Maps, etc.
- Technical and commercial clarification
- Creating a package from a set of purchase requests (MR)
- Distributing the purchase requests among the vendors and manufacturers in accordance with the AVL of the project
- Receiving the financial and technical proposals (bids) and sending them the engineering department for further consideration
- Examining the proposals (bids) and setting the TBE in order to evaluate the technical competency of the bidders
- Defining the vendors’ list of documents (VDR) ,checking and distributing them to the engineering department for further consideration
- Receiving progress report related to the document production phase in the purchase phase
- Observing the last status of the purchase requests sent to the procurement unit
Managing the tenders and enquiries in the PPMS
- Preparing the commodity fabrication/purchase tender documents
- Making the Long Bidders List (LBL) and Short Bidders List (SBL) of the companies
- A standard system to Inform the vendors and manufacturers to participate in the tender and exchang the required documents between the parties
- Conduct enquires from manufacturers and vendors about the tender and receiving their technical and financial proposals
- Clarification system for exchanging information and resolving possible ambiguities related the technical, and financial proposals of the parties
- Receiving the TBE from the engineering unit (via the engineering module) and preparing the Unpriced CBE and Priced CBE
- Keeping a record of the correspondence and any detailed information of the bidder companies in the engineering unit
- Scoring system, selecting and announcing the tender winner
Managing the contract affairs in the PPMS
- Writing and registering the contracts
- Defining the contract guarantees as well as the guarantee conditions of the items
- Finalizing the contract, approval process, signing, and announcmeent,
- Defining the registry of the minutes related to the contract commencement such as the kick-off Meeting
- Registering the payments to the manufacturer company
- Defining the activities of each contract and registering the schedule
Managing the manufacturers and vendors
- Defining and importing the databank of the manufacturer and vendor companies via EXCEL software
- Defining and importing the list of manufacturer and vendor companies approved by the employer in a project (AVL)
- Defining the third-party companies such as forwarders, inspector companies, etc.
- Defining an unlimited tree structure in order to group the manufacturer and vendor companies based on their fields of activity.
- Registering the result of primary assessment of the manufacturer and vendor companies via PQ forms (Prequalification Forms)
- Evaluation of companies invited to tender
- Obtaining the history and performance quality of the manufacturers and vendors in previous projects
- Activating the web-based system of the companies in order to perform the transactions (trades) through it
Managing the information related to fabrication, inspection, and shipment phases
- Recording the exact date of milestones, manufacturer/vendor companies’ reports, uploading the relevant files during the fabrication stages
- Calculating the fabrication progress from the reports provided by the manufacturer company
- Recording different stages of inspection during the fabrication, supply, and pre-shipment phases
- Recording the manufacturer company's readiness for inspection (Inspection Notifications)
- Recording the inspection reports of the third-party company (inspector) in the PPMS
- Defining the Part List and preparing the Packing List of the deliverable items for shipment
- Recording the stages and documents of shipment (domestic and foreign), costumes ceremony and uploading the relevant files in the PPMS
Item delivery process
- Observing the Packing List at the time of loading from the manufacturer factory
- Recording the documents related to the delivery of items to the site warehouse
- Saving the loading data in the warehouse
- Saving the preservations information of the items till the opening
- Recording the opening report or OPI (Open Package Inspection)
- Recording the results of the opening report or OSD (Overage/Shortage/Damage)
- Recording and matching the opened items with the list presented by the manufacturer company (Packing List)
- Recording the approved items to enter the warehouse through the MRS form
- Controlling the post-delivery instruction manuals such as installation & operation, training, testing, guarantee release time, guarantee period, and after-sale services
- Connecting to the warehouse module
Controlling the project and managing the resources of commodity purchase and supply projects
- Defining all activities related to all stages of the fabrication/purchase process
- Allocating a weight factor to each activity
- Calculating the progress of purchase packages separately, and calculating the progress of the whole purchase project
- Calculating the progress of the engineering phase of purchase by engineering module and establishing a connection between two systems
- Monitoring the supply status of the items at any stage
- Recording the items' supply schedule, observing the delays, and taking actions to expedite them
- Managing the parties' commitments including delivery times, payments, guarantee release, etc.
Correspondence system and its connection to the PPMS
- Automatic connection to AFAM's PATS software (Project Automation System), which is provided as a separate Module
- Registering the letters of the project
- Establishing an automatic connection between the activities and the correspondence at the time of automatic registration
- Establishing a connection between the correspondence and the activities by the user (client)
- Classifying various correspondence (letters, minutes, email, etc.) based on the type of correspondence (e.g. input, output, internal, miscellaneous, etc.), technical disciplines, and other key information fields in the project
- Recording various actions on each correspondence and allocating it to the individuals in the project
- Recording the Action Report on the allocated actions with a capability of reminding and alarming
Reports and dashboards in the PPMS
- Reports related to the manufacturers and vendors separated based on the field of activity
- Reporting the last status of the purchase requests
- Receiving the reports of the overall status of the project
- Observing the fabrication and inspection status
- Receiving statistical reports related to numerical status of the project purchases
- Observing the delivered items
- Reporting the status of project contracts
- Reporting the progress status in engineering phase of purchase
Vendors system
- Allocating a username and a password to the companies in the SBL.
- Getting informed of the invitation to the tender via Email
- Accessing the tender documents and responding the invitations through the PPMS
- Uploading the relevant files for participation in the tender
- Sending commercial and technical proposals (bids) and uploading the relevant files through the PPMS
- Performing the Clarification Process through the PPMS
- Uploading the fabrication reports
- Sending the Inspection Notifications to the procurement unit through the PPMS
- Registering and announcing the Release Note and the portable Packing List
- Announcing the actions of the shipment phase and relevant documents